サービス体制
短納期対応
短納期の本質
そもそも短納期と言いましても、どのくらいを短納期と言うのでしょう?例えば、ある設計した部品をCADデータと共に10個発注し、受注後1週間で手元に届いたとします。これを、短納期だと評価いただけるお客様もおられますし「一週間もかかるの?」と全く評価されない場合もあります。
また、加工会社側でも納期の認識はさまざまであり、とりあえず回答納期は1週間を基本としている会社もあれば、新規品なら最短でも2週間と答える加工会社もあります。
いずれにせよ短納期への取り組みは各加工会社で工夫を重ねていると思います。
ウシオでも下記のような取り組みを行っております。
ウシオの短納期対応への取り組み
スタッフ 7名 に対し、
機械 | 台数 |
---|---|
CAD/CAM | 4台 |
レーザー加工機 | 2台 |
タレパンプレス | 1台 |
ブレーキプレス | 6台 |
油圧プレス | 2台 |
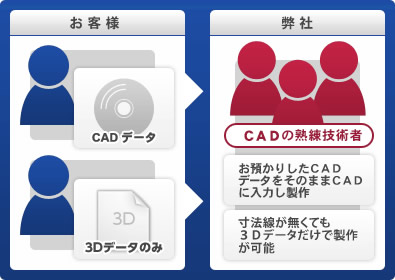
ご発注から納品までを納期と呼びますが、実際加工する会社ではどのように納期を算出しているのでしょう?実は、どの加工会社も一つの商品を製作するにあたり、実際の所要時間は少ないものです。
実際に製作する時間よりも、受注の順番と納期の順番を段取りしながら調整し、おそらくこれだけの日数があれば調整が可能で納期どおりに納品ができるであろう日程をお客様に回答しています。
このご回答する際のターゲット納期が、各加工会社の経験値により大幅な違いとなって表れます。
見積もりをする段階で材料の確認をし、受注後には即製作方法を決定し、2次加工の段取りをし、製作を進めるという作業が、どれだけスムースかつスピーディーに行えるか?これが試作専門会社の特色となります。
発送体制の重要性
それから、もう一つ短納期対応に欠かせない重要な要素があります。それは、集荷・配達をお願いしている運送会社さんです。
例えば、近くに運送会社の営業所があれば出荷条件は有利に働きます。
大阪ということもあり、ウシオの近くには各社営業所が点在しておりますので、到着の早いご指定運送会社便にて発送致します。
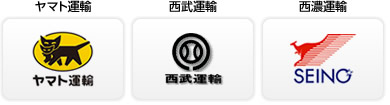
その他の運送便につきましてもお気軽にご相談下さい。
お客様側からの納期短縮のポイント
材料
一般的に流通している材料は、基本的に次の日に入手が可能です。しかし、特殊で流通の少ない材料は、入手が困難となります。
特に試作の場合、使用量が1枚など、ごく少量の為、材料屋さんも商売にならず、なかなか入手しにくい場合があります。
例2:ばね材料などの、硬度指定が特殊なもの。
例3:特殊な表面処理鋼板。
上記のような材料は入手までに時間がかかります。
少量で費用もかからないので事前に手配をかけておく。もしくは、発注者側で材料を入手し、支給することで、材料調達にかかる納期を短縮することが可能です。メーカーさんからお声がけいただいた方が早く入手できる場合があります。
データ支給方法
最近は、FAX図面のみで製作依頼をされるお客様が減ってきましたが今でもゼロではありません。弊社では、できるだけCADデータの支給をお願いしています。
過去からの図面手配の方法を整理してみます。
1.図面手渡し
2.図面FAX
3.2DCADデータFD渡し
4.2DCADデータメール送信
5.3DCADデータメール送信
図面の手渡しから始まり、現在では、
・2Dデータ
・3Dデータ
・PDFファイル
の3点セットをメール送信する手配方法が大半となっています。
この3点セットで手配をするメリットは、加工側の不明点が無くなり、時間ロスがなくなることです。
例えば、2D図ではどうしても理解できない箇所がある場合でも、3Dデータを見れば即解決します。
もし、3Dデータの支給がなければ、発注者に確認をとります。ところが発注者が席を外していると、回答待ちの時間が発生してしまいます。
更に、2D、3DのCADデータを支給されていても、例えば文字化けして読めない場合、PDFファイルがあれば即解決となります。
確かに3つもデータを用意するのは面倒ではありますが、発注側が少しの手間をかけることで、後の問い合わせが減り納期遅れを回避できますし、設計者自身も落ち着いて次の仕事にとりかかることができ、時間効率を上げることにもなります。
試作要素の柔軟性
試作時点での素材切断方法には、主に下記3つがあります。
・シャーリング加工
・レーザー加工
・タレパン加工
シャーリング加工は、直線しか切れませんが、1m~2mの幅を一瞬で切断できますので、アバウトな寸法切りであれば、この方法が早くなります。
次にレーザー加工ですが、現在の板金加工では最もポピュラーな加工方法であり、CADで描いた線の通り自由自在に切断できます。
最後にタレパン加工ですが、これはさまざまな形状の金型で必要な形状の外側を抜き落として残った部材が商品になるという加工方法です。
それぞれ長所と短所がありますので、案件に沿う加工方法を選択することが、価格や納期の価値の合致に繋がります。
シャーリングで加工可能な形状をレーザーで加工すると割高になりますし、寸法公差が厳しいものをシャーリングで加工すると寸法公差内に収まらなくなります。
その他の加工方法として、ワイヤー加工やエッチング、簡易金型での抜き落としなどもあります。
例えば、「銅板」は、レーザー加工ができません。
なぜできないか?理由を簡単に説明しますと、レーザー光線が材料に反射して機械自らを焼いてしまうというような理由です。
ですので、こられの材料の試作依頼には、レーザー加工以外の加工方法にて加工を進める必要があります。そのような場合に、ワイヤー加工や簡易金型での抜き落としなどが必要になってきます。
例えば図面上は「銅板」になっているが、試作時点では「りん青銅」や「真鍮」、「アルミ」でもよいという場合、それらの材料で指示をすれば、本来レーザー加工以外での製作検討をしないといけないところ、レーザー加工が可能になるため、納期が早くなり価格も下がることになります。
試作形状の柔軟性
絞りとは、通常は平面である板を変形させ、凹凸をつけることを言います。板金部品になぜ絞りが必要なのか?
まず、最も仕様目的の多いのが強度を目的とする補強です。板の厚みが薄くても、補強することにより強度を増すことができます。
板の厚みを増すことなく強度を増すことができれば、軽量化と材料費のコストダウンに繋がります。
更には、本来別部品を製作しスポット溶接などで接合していた部分を、ブリッジ形状にすることにより一体加工が可能となり、こちらもコストダウンに繋がります。
しかし初期の試作段階で、このような加工を盛り込むには簡易金型などを含めコストアップと工期アップとなります。
初期試作段階では、このような形状が必要でない場合、複雑な絞り部の加工を省いたり別部品で対応したり、溶接構造を指示することで開発費の削減と納期短縮が可能になります。
2次加工の柔軟性
塗装やめっき、シルク印刷などの表面処理や、例えば一部分だけを切削加工する必要があるなど、実際に量産品になれば必要な加工も、試作の時点では必要でない場合が多々あります。
特に必要でない加工を省くことにより、納期の短縮とコストダウンが可能になります。
余裕を持った生産計画
なにより生産計画は重要です。さまざまな事情があれ、無理な計画を立てますと、すべてがぎりぎりの日程で進むことになります。
どの行程も問題なく終了すればよいですが、もし途中で何らかの問題が発生し、例えば再製作などになってしまいますと、当初の予定よりも大幅に完成が遅れてしまいます。
また、急ぐがゆえ、加工会社との打ち合わせを経て、製作予算を検討する時間もありません。
試作はプレスのようなリピート品ではなく、毎回図面を見てから製作方法を考え、納期を算出し製作を進めます。
途中、考えていた方法では寸法が出ず、最初からやり直しとなるリスクもあります。
そのような業態を考えますと、ある程度余裕を持った生産計画をする方が、スムースなプロジェクトの進行を確保できることになり、また品質、コスト面でもメリットを生む可能性が高くなります。
日程に余裕があれば、途中で寸法変更などに気づいても、当初のままの納期内に盛り込むことができる場合も多々あります。